A Simple Guide to Choosing
Packaging is a consolidated need for product protection during handling, blocking unstable products placed on pallets, protecting the product from atmospheric agents and any situation that requires the use of film external to the product.
There are many types of packaging, Effe3Ti mainly deals with winding, heat shrinkage in chamber furnaces and systems strapping and canning.
Indispensable for the Customer who wants to consider purchasing a machine pallet wrapper, is having an easy-to-use guide to help you choose the right machine.
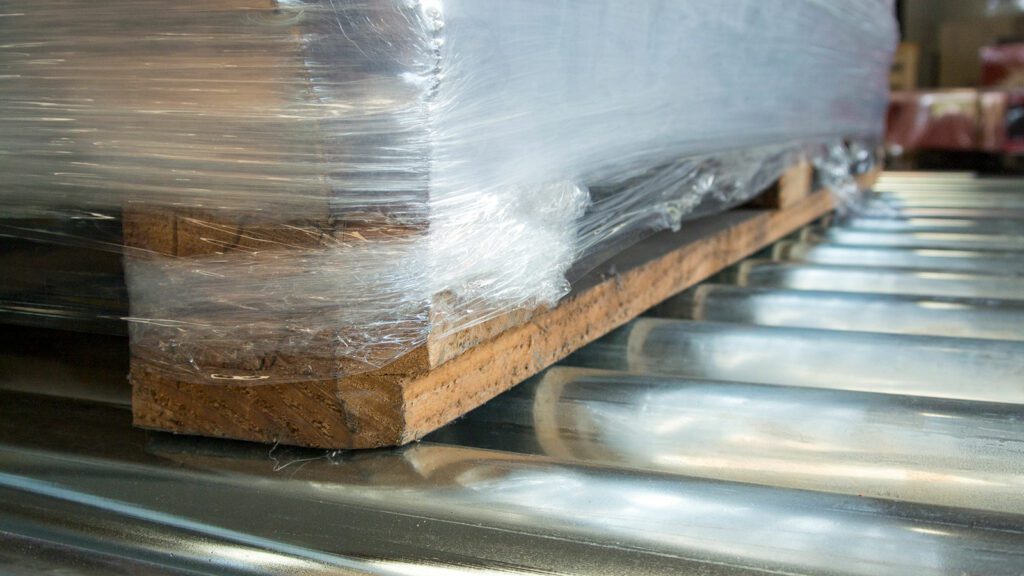
Automatic or Semi-automatic?
The first factor to consider when choosing a machine is the amount of work it will be subjected to. Generally speaking, you can choose a machine semi-automatic when the amount of work reaches a maximum of 20 pallets/h processed, while a machine automatic It turns out to be the right choice for 50 pallets/h and beyond.
- The automatic machines are characterized by completely autonomous operation with automatic loading, starting, cycle and unloading. The automatic machine must be protected with nets and with “muting” safety barriers as required by current legislation in order to safeguard the operator during the cycle phase. Effe3Ti supplies, upon request, automatic lines complete with chain or roller transport, with all the safety systems required by the regulations (including non-EEC EN markets).
- The semi-automatic machines are characterized by the versatility of use in any condition the Customer must operate, they have the possibility of having a "forkable" frame to be easily transported from one production department to another and there is also the version for a rotary table shaped to accommodate forklift forks. The loading and unloading of the package to be wrapped are the responsibility of the operator as is the cycle start button located on the control panel on the machine column. Semi-automatic machines do not require the use of safety nets since the speeds of the movements in play on the machine are all lower than those defined by the regulations and, during the design phase, solutions were studied to make each movement safe.
Table or Rotating Arm? …or Self-Propelled Robot?
The second factor that we can consider is the choice of the type of pallet wrapper. The two main large families include a rotary table or a rotating armIn the first, the pallet of product is loaded onto a table that rotates to allow for wrapping, while in the second, the pallet remains stationary while an arm rotates around it, applying the stretch film.
- We generally use a machine with rotary table when the weight of our pallet of product to be wrapped does not exceed 1500/2000 kg. The load capacity of a rotating table has a limit and even if reinforced above a certain weight it becomes necessary to turn to another type of pallet wrapper.
- We generally use a machine with rotating arm when the weight of the pallet to be wrapped exceeds 1500/2000 kg. However, this is not the only reason. In fact, although table machines, especially automatic ones, are equipped with very advanced rotation management systems, it may be right to orient yourself towards the rotating arm when we are dealing with very unstable products.
A separate discussion must be made regarding the self-propelled pallet wrappers (robots). These special machines, in fact, are equipped with wheels and powered by high-performance batteries that allow them to be moved wherever you want. They are not “minor” machines at all, in fact they can automatically wrap the pallet of product according to advanced wrapping programs. Choosing a self-propelled wrapping machine allows you to wrap your products without having to move them.
Do we save stretch film?
It is not only an ecological choice to opt for a saving of stretch film. The consumer product has in fact a significant impact on the company's logistics expenses and represents a "hidden cost". Let's see what the possibilities are.
Film consumption Depends from the type of reel holder installed on the pallet wrapper. The economic model has a reel holder group with pre-stretch (this is the name that defines the group that supports the reel and dispenses the processed film between the rollers on the package to be wrapped) mechanical or with magnetic brake. This model has only the tension adjustment of the film between the machine and the package.
The best performing model (also in terms of film consumption) is definitely the motorized pre-stretching, available with one or two engines.
The motorized pre-stretch with a motor has a fixed pre-stretch ratio, obtained by distributing the motion of the rollers with toothed wheels. Different types of pre-stretch ratios can be obtained (100%, 150%, 200%, 250%, 300%, 350%) based on the reduction ratio between the gear wheels (ratio that can be modified by replacing the pair of gears) i.e. if 100mm of film is unwound from the reel, after passing between the motorised rollers it will reach a length of 300mm (in the 200% ratio) with a significant film savings.
The pre-stretching with two motors easily reaches a ratio of 400%.
This solution also allows to reduce the tension of the film on the package and therefore the wrapping of unstable and non-homogeneous products (the wrapped pre-stretched film continues to recover its elastic elongation for about a day. Obviously the pre-stretched film will also have a plastic phase that will allow it to stretch without return and without breaks during the wrapping cycle).
The film can be placed manually on the package to be wrapped (in semi-automatic machines) or a pair of clamps locks the film on the rotating table for dragging during the wrapping cycle.
Film cutting can be manual or automatic with hot wire enabled only during the cycle, at the pre-set time.
The sealing of the film flap that remains at the end of the cycle is done either manually or automatically based on the Customer's needs. The sealing pad, at a temperature of 115°C, automatically seals the film flap on the film previously wrapped on the package. If the package to be wrapped is not homogeneous, a contrast plate for the welder is placed between the pad and the package in order to protect the product.
What do I need?
Having said all this, which is the best machine? In reality, the most sensible advice is to tell one of our qualified technicians what you need, who will certainly be able to suggest the right solution. There are countless needs and just as many possibilities to manage them, perhaps combining the pallet wrapper with one or more accessories that make it perfect for the job that needs to be done.
A (incomplete) list in short:
- Easy – semi-automatic machine, rotary table, mechanical, magnetic brake or motorized pre-stretch.
- S140 Plus – semi-automatic machine, rotary table, mechanical pre-stretch
- S140 Advanced – semi-automatic machine, rotary table, mechanical pre-stretch with magnetic brake, key control panel with display
- S300 – semi-automatic machine, rotating table, motorized pre-stretching (1 motor), control panel with keys and display
- S350 – semi-automatic machine, rotating table, motorized pre-stretching (1 motor) with “touch screen” control panel
- S500 – semi-automatic machine, rotating table, motorized pre-stretching (1 or 2 motors), “touch screen” control panel with automatic film welding and cutting system
- S2300 – automatic machine, rotating table with integrated motorized transport, motorized pre-stretching (1 or 2 motors) “touch screen” control panel
- Rotax 3300 – semi-automatic machine with rotating arm, motorized pre-stretching (1 or 2 motors)
- Rotax 5300 – automatic rotating arm machine, motorized pre-stretching (1 or 2 motors)
- Oscar – pallet wrapping robot, mechanical, magnetic or motorized pre-stretch brake.