In un giorno normale, Tuatara Brewery (NZ) imbottiglia, etichetta e imballa 7000 litri della sua premiata birra. Eliminare il lavoro manuale di avvolgimento grazie a Spinny S140 ha allentato la pressione nel fine linea.
When Michael Bailey started out as a warehouse worker at the Kapiti Coast Brewery, he wrapped pallets by hand, a process he describes as “a mission and a 1/2”.
There were two people dedicated to this job at the time, one preparing the pallets and the other hand wrapping them and then placing them on his line. But when new production systems increased the speed at which beer was bottled and labeled, the stress began.
“We were starting to feel the pressure,” Michael admits. While no stranger to the manual labor involved in the job, he notes that “hand-packing was a struggle for the new employees—they just couldn’t keep up.”
Investing in a system of semi-automatic winding Spinny S140 It was an easy decision to make.
Carico protetto con Spinny S140
The biggest challenge in transporting liquids, especially in glass bottles, is that the load must be securely attached to the pallet.
Previously, manually wrapping pallets was a balancing challenge. “The boxes moved a lot in transit and some of the boxes slipped,” says operations manager Hamish Allan. “With the new system, that’s all changed.”
“Spinny S140 ha diverse configurazioni per la tenuta e gli strati di avvolgimento”, dice Michael, “tutto è solo preimpostato in modo da caricarlo, legarlo al pallet, scegliere l’impostazione. Tutto qui”.
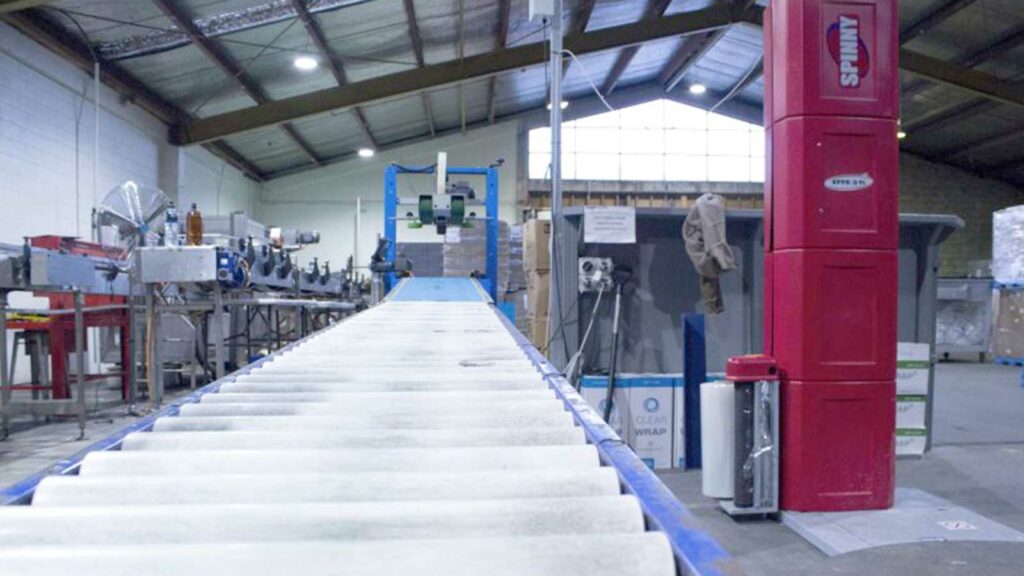
Time saved
Getting the tension right to keep the product stable was a challenge with the old system. “It took a good two or three minutes to wrap by hand,” says Michael. “Because the boxes could move around in transit, it took a lot longer to wrap. You also had to avoid overloading the line, so it was hard to be sure each wrap was done properly. Spinny definitely saves us a lot of time – and stress.”
Work done
The Spinny S140 Advanced features four programmable wrapping cycles, perfect for distribution centers shipping mixed pallets.
“You can set the tension, you can program how many layers of winding you want,” Michael says. “It’s basically all done, you do something else and come back when the machine is done. We save one person’s labor.”
Constant peace of mind. Spinny’s work was seriously tested in the 2016 Wellington earthquake. After checking the warehouse for damage, Tuatara was surprised (and delighted) to find that not a single bottle had broken.
“We haven’t had any real damage,” he says. “Some wine stores along the road have had product slide and have suffered a lot of damage.”
This is an achievement worth toasting. Perhaps with a good New Zealand beer.
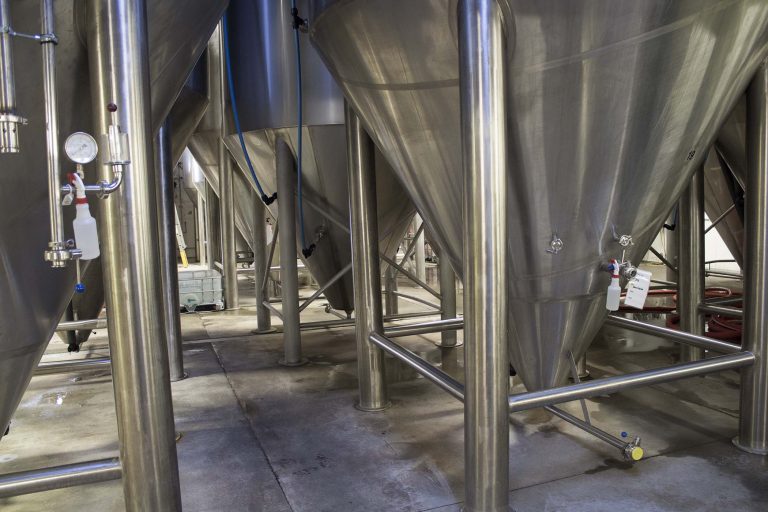